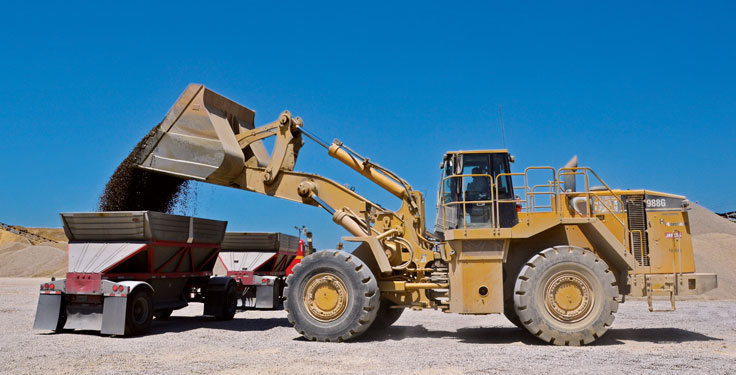
Finding enough skilled labor in the industry has been a challenge for years.
Construction Industry Resources, a data firm, estimates that the industry could face a shortage of at least 2 million workers through 2025.
The industry has seen the effects of this labor shortage for quite some time, and funding from the Infrastructure Investment & Jobs Act is sure to exacerbate it. But before the bill became law in 2021, project owners were reporting that up to 25 percent of material deliveries to sites were late or incomplete.
In some cases, the combination of higher hourly rates, premiums and incentives – plus overtime payments – resulted in labor costs doubling pre-COVID levels. Difficulty accessing skilled and experienced people led some owners to report project delays related to issues around the quality and productivity of on-site work.
According to the National Center for Construction Education & Research, about 41 percent of the current construction workforce – including those in management roles – will retire by 2031. So it’s vital to recruit new talent into the industry. Construction, however, isn’t the only industry desperate to hire.
To avoid a decade or more of rising costs, falling productivity and project delays, companies must take bolder, more aggressive approaches in their technology investments so they can not only attract younger people, but retain the new pool of talent.
Lagging productivity threatens success
To reduce the blow of a work shortage, companies can turn to technology to make the process of building new infrastructure more efficient, cost-effective and to reduce – where possible – the amount of labor required to complete projects.
SjaSmarter execution management, enabled by digital technologies and analytics techniques, could drive better, faster decision-making during project delivery. Real-time data collection, for example, gives project managers earlier, more detailed insights about progress, allowing them to intervene more effectively to maintain productivity and keep projects on track.
The materials the construction industry makes, hauls or buys are almost always on the critical path for the end customer. It’s crucial to react quickly to bottlenecks that might throw a wrench in operations and throw jobs off schedule.
Many innovative companies are increasingly investing in software that allows them to track and trace materials from the moment an order is made all the way until the material reaches the jobsite – and afterward, during the payment process. Seeing more and knowing more as materials and data flow helps to ensure jobs are completed on time and in budget.
Improve communication & data sharing
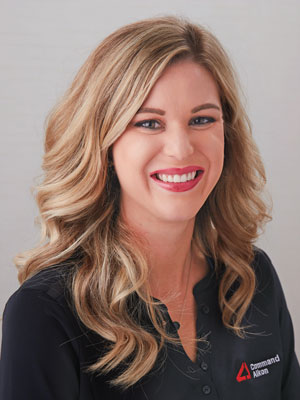
With improved communication, materials are easily located and on track for use at the right place for the right operation.
Clear visibility into traceability of material properties and orders ensures that products arrive in the best possible condition, reducing delays and productivity lags. Businesses can ensure complete delivery and materials traceability and uncover smart insights for decision-making with connected logistics solutions.
Drivers have the information they need at their fingertips – including their next ticket – so they can be back on the road to their next job as soon as their current delivery is made. To create more efficient fleet operations, companies are using tracking solutions to map the location of trucks in real time, as well as telematics devices to monitor truck performance parameters such as engine speed and coolant temperature.
These devices provide visibility into fleet operations, monitoring the loading and unloading of trucks, as well as wasteful idling while in traffic or at a jobsite. Once managers understand the cause of nonproductive hours in their operations, they can revamp processes for greater efficiencies by using route planning and mapping solutions to avoid traffic delays.
Waiting on paperwork hampers productivity. If processes are automated so operations flow quickly and easily, workers don’t have to sit around and wait for paperwork to arrive.
The 2017 “Everyday Counts: Innovation Initiative” issued by the U.S. Department of Transportation combined e-construction with so-called construction partnering (E-C&P) to accelerate the adoption of electronic processes. E-C&P calls for training and aid for decision-makers and other key stakeholders, such as state departments of transportation, contractors and consultants.
Electronic material ticket management systems automate manual practices across the industry, eliminating tangible paper tickets while addressing the challenges created by outdated methods for tracking materials and truck assets. Many successful e-ticketing pilots have occurred nationwide since the implementation of the “Everyday Counts” initiative, and the exchange of electronic ticket data has bridged the e-construction gap that exists between public agencies and building materials suppliers.
Time for change
Getting rid of paper-based, manual processes and implementing digital solutions should be a part of any company’s strategy. But technology purchases are only as good as the people using the technology.
Acceptance and adoption of new processes must be handled carefully. Change management practices should be followed so users accept new tools as benefits rather than threats.
Change management best practices reveal that the highest rates of adoption come when a company starts with a bottom-up approach, training daily users first so they engage with the technology and building up their experience.
It helps to have an internal champion who not only promotes the use of the technology and its benefits, but also builds camaraderie and inspires the full team. Successful implementors will encourage team members to keep moving forward.
With the right change management processes, effective training and patience, technology successes should drive additional successes.
Karli Langner is public relations manager at Command Alkon.