Scott Construction Inc. in Lake Delton, Wisconsin, is one of the state’s leading asphalt surfacing companies – and its largest chip seal contractor.
To support the amount of chip seal work the company performs throughout Wisconsin and Minnesota (regional suppliers couldn’t keep up with the demand), the company began mining granite out of the new Pine Valley Quarry in Neillsville, Wisconsin, in 2015.
With the new quarry, Scott Construction can control quality and access to its chip seal products. The company shoots raw granite and crushes it down to 5/8-in.-minus and then screens it and crushes it down again to 1/2-in.-minus. The company then washes that and crushes it down to 3/8-in. and 1/4-in.-minus product. The remaining byproduct is then used for hot mix and concrete.
The company can also load upwards of 150 trucks a day, depending on the output/demand.
Keeping up with demand
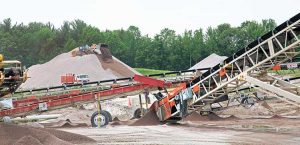
By early June 2016, the company had tripled its production out of the quarry compared to all of 2015. Much of that workload is performed on the shoulders of its wheel loader fleet. The company uses both a Case 721F wheel loader and a Case 821E wheel loader in the crushing stages of production.
From there, a Case 1021F wheel loader takes over and handles the bulk of truck loading and material handling activities.
“The 1021F is the key piece in everything that’s going here,” says Steve White, operator, Scott Construction. “It’s irreplaceable. The 1021F has been the heart of our operation here.”
Scott Construction handles 350 tons of granite each hour during the course of a 14-hour day. Daily tonnage often exceeds 4,000. With such a heavy workload, Scott Construction worked with Wisconsin dealer Miller-Bradford & Risberg to equip the site with a high-capacity wheel loader.
The 1021F is powered by a 296-hp FPT engine and is driven by a four-speed Powershift transmission with heavy-duty axles with a locking front differential. One of the first things White noticed with the machine was its climbing ability. After dealing with significant overflow, the company recently built ramps to improve on-site stockpiling.
“The 1021F is unbelievably able to climb grades that you wouldn’t assume it would,” White says. “We berm it up good and we’re stacking it up … that’s been a big improvement.”
Cutting back on fuel
In such an active environment, fuel efficiency was also important, and the 1021F wheel loader features selective catalytic reduction (SCR) technology.
“Compared to [a competitive machine], we’re using almost 230 gallons less a week of diesel fuel doing the same job,” White says.
The SCR technology gives operators a faster throttle response, while also maintaining low exhaust temperatures and improving fuel economy by as much as 10 percent (compared to previous generations). There are also no diesel particulate filters to replace and no downtime associated with regeneration.
The 1021F also features four programmable power modes: “eco” for maximum fuel efficiency, “standard” for quick loading, “max” for aggressive digging and “auto” for engine output that responds on the fly. A standard engine shutdown feature is also available to further save fuel by limiting engine idle time.
“[With the four programmable modes], we’ve increased the amount of production and decreased the amount of fuel used to get there, so it just works,” White says.
Each operator also focuses on cycle time and efficiency. Charles Hudzinski, loader operator, Scott Construction, notes the loader helps him transition from dumping to loading functions with the return-to-dig and return-to-travel features. Each allows the operator to hit a button, which automatically returns the loader arms and bucket to a pre-selected spot, freeing the operator up to focus on the transition and/or other required tasks.
“When I’m backing away from the truck, I push the lever all the way ahead to lock it in, and it’ll come down to a certain height from the ground and stop on its own, so that I can talk to the truck driver or whatever I have to do without my hands on the control at the time,” Hudzinski says.
Hudzinski also notes the ease of transition from forward to reverse, which is critical in shortening cycle times in loading applications.
“It’s about the smoothest one I’ve run,” Hudzinski says. “You don’t really notice it when you’re shifting forward to reverse.”
Scott Construction loads out 25,000 to 30,000 tons of material each week, in addition to the 4,000-plus tons they run through the plant and stockpile each day.
Smooth ride
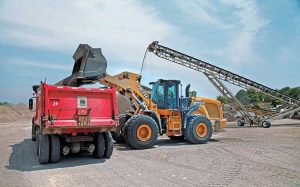
The 1021F has Case ride control, which provides a cushioned ride that can handle a large volume of material at increased speeds. Ride control automatically dampens loader arm bounce at elevated speeds – reducing spillage and giving operators full control of their load retention and comfort.
“The 1021F is a lot faster and smoother with ride control on it,” White says. “It rides smoother than the [other machine we had], so we were able to increase speed and volume.
“In some spots, we have ruts that are washed into the pit floor that are a foot deep,” White continues. “With ride control, you can take a loaded bucket full of material, and the operator can drive across it and not even notice it. It won’t spill a drop, so that ride control is a must.”
A typical day for Scott Construction starts at 6 a.m. and goes until 8 p.m. or later. Working those long hours can wear on operators if they’re not comfortable. The 1021F wheel loader features a large cab and an iso-mount cab design that reduces external noise and vibration to create a clean, quiet operating environment.
“We compared this machine to our other models that we used to run, and the Case is the best ride we’ve ever had in any wheel loader we’ve ever owned or leased,” White says. “You don’t get fatigued from turning the steering wheel or running your bucket or your boom up or your bucket leveler. When they designed this machine, they designed it for the comfort of the operator.”
Another hallmark of the 1021F is its visibility. The wheel loader features floor-to-ceiling glass windows and excellent visibility to the rear of the machine.
“You can get so much closer when cleaning around conveyors,” White says. “We’re in granite rock, so you don’t want to run on rocks and cut your tires: You can physically see how close you are to anything. It’s been an improvement that we like.”
Keeping machines up and running
Another benefit of the 1021F is its easy maintenance. The wheel loader features easy-to-read site gauges, a standard power-tilt hood and grouped, ground-level access to most service points.
“We just did an oil change on the 1021F, and it took the operator less than an hour and a half to do complete service on the machine,” White says. “You roll the hood up, and everything is in direct eyesight; you can see everything you need to service. The filters are easy to get to. Overall, the serviceability is phenomenal.”
Much of the service and support is provided by Miller-Bradford, who services the company throughout Wisconsin from a number of locations. It’s the confidence in Miller-Bradford that sealed the deal with the 1021F.
“Miller-Bradford is a four-star operation,” White says. “I’ve worked with them for the past 32 years. I know Charley [Rule, service manager] in Madison quite well. He’s a phone call away 24 hours a day. He’s come to my rescue so many times I can’t tell you. If the 1021F is our heart, they’re our blood … and without both, it wouldn’t work. Miller-Bradford, at least for me in my division, is our best vendor.”
Andrew Dargatz is the brand marketing manager at Case Construction Equipment.