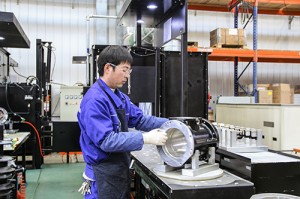
customers to choose custom designs.
Photo: Martin Engineering
Martin Engineering launched a new manufacturing process for building its industrial vibrators. The company has already completed two cells, which are operating in the U.S. and Asia. According to Martin Engineering, the process delivers repeatable close-tolerance results for product uniformity, cuts manufacturing time and reduces the physical demands on employees.
“Our goal is to avoid a business model of centralized manufacturing and then trying to sell products across the globe,” says Robert Nogaj, vice president of operations at Martin Engineering. “This new process gives us the capability to centralize the innovation and design capabilities for our vibrators in the U.S. and manufacture them to the highest quality control standards at the local level.”
The company’s manufacturing process allows customers to choose custom designs, says Nogaj, which allows them to maximize value without extended lead times.
Using new lifting methods to ease the movement of heavy cases, the manufacturing process also reduces strain on employees. In addition, run testing and electrical confirmation are also now done in-line during the process.
“The whole process is much faster and extremely repeatable,” says Nogaj. “We’re relying far less on human judgments, using special fixtures and tooling, as well as automated steps for mixing and curing epoxy, packing bearing grease and performing other key other functions.”
During the process, all the data is stored in a computer, which allows users to trace every unit back to its individual components. According to the company, the new process delivers high-mix, low-volume production without sacrificing speed or quality.
The company plans to build its next two manufacturing lines in South America and Africa this year.