The following transcript was edited for brevity and clarity from one of two concurrent Jan. 31 discussions at the 2025 Pit & Quarry Roundtable & Conference at The Wigwam Resort. Read Part 2 from the Roundtable here.
KEVIN YANIK (PIT & QUARRY): How would you characterize the industry’s record on safety today? What improvements can be made to genuinely make operations safer?
For suppliers: How are you supporting the producers in the industry in their effort to operate more safely?
RAYMOND SLAUGHTER (LUCK STONE): We use a value-based safety program. We’ll actually take a step back now because of the new employees we’re bringing in, and the culture is built over time.
We’re reinvesting in the value-based safety program, which is making tough decisions and giving people the awareness to the hazards. You can have the safest site, but if they’re not aware then it’s hard to make the right decision.
We’re kind of doing it both ways. We’re employing new technology, rolling out all sorts of digital pre-work shift forms where we can pull all information from. But one of the key takeaways is just backing up and trying to introduce the new people to what it means to be making the right decisions when it comes to their own safety.
DOMINIC NASSO (BUFFALO): We’re putting a lot of time into magnetic liner technology, for example. It’s out there, but it’s evolving for liners. We want to get people in and out of machines quickly – no bolting, no welding – and we’re working with different materials for different applications to be more widespread.
Getting in and out of the machine safely is one of our priorities in line with technology.
KRISTIN SWEENEY (US AGGREGATES): I’m going to echo some of what Raymond talked about. We’ve had a shift in workforce experience and the new miners coming in.
Raymond hit it right on the head: Miners don’t know the hazards they are exposed to. The hazard recognition is really lacking, so we’re taking a pretty strategic approach in reviewing all our task training, talking about a tiered approach to it.
On a piece of mobile equipment, for example, Level 1 is you’ve been trained on how to do the pre-shift to turn it off. Level 2 is basic operation. Level 3 would be more specialty application, so how do you use an extractor.
In Level 1, you can turn it on, and you maybe raise and lower the boom. Level 2 is you can dig a hole, and you can load a truck. Level 3 would be, maybe, doing some scalping operations or scaling operations on a highwall, or working your water.
So, it’s really going back to say our task training has to start more basic than we’ve ever had to start before.
I agree with the digital training logs and having that available for our teams to be able to pull that up. I know we’ve seen booklets in the past. We’ve seen all the things where you attach them and give them that reference material.
We’re utilizing some software where it’s available for our team. So, if they need to reference that material, it’s at their fingertips. They don’t have to go to the office and try to dig through a booklet.
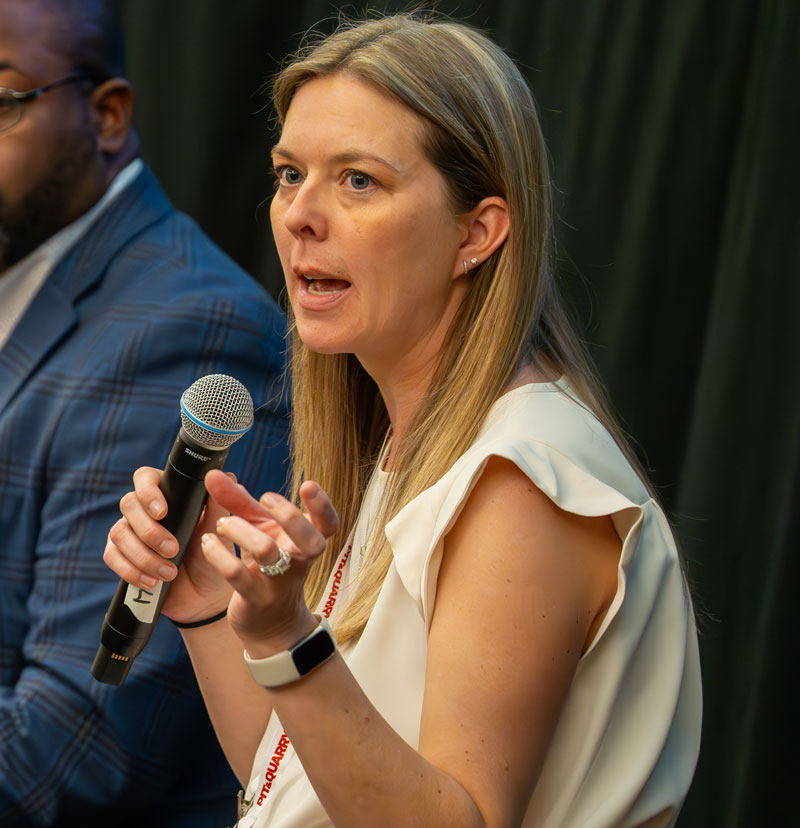
CHAD GREENFIELD (SYNTRON MATERIAL HANDLING): Most everything we’re doing from a supplier aspect is technology related. All our technology is dual focused. It’s to help with production efficiencies, but it’s also to help with safety.
Primarily, it’s getting people away from the equipment so they can remotely monitor, know when things are going wrong, and understand what’s going on without having to be at the equipment.
Some of the other areas of focus are on preventing catastrophic things like belt fires, understanding when equipment is potentially having an issue before we get to an issue like that. This is primarily technology related.
GEOFF HAWKER (HAZEMAG): First, I like what Chad said about getting the operator away from the equipment. That’s going to be a push for us. That’s a big part of modern-day design, and it’s a big help.
Secondly, some of the producers mentioned the issue of training and getting new miners up to speed. I would just say at HAZEMAG – and I know many of our competitors and fellow suppliers here – would welcome the opportunity to come on-site and provide training. Any time you guys are planning training programs, I would encourage you to reach out. For us, it’s a big part of what we offer. I know we’re not alone in that.
RYAN MORALES (GULF COAST SAND): We’re employing technology solutions directly related to safety and a lot of the documentation around it. This could be sent to us as SOPs (standard operating procedures) or just having a calendar of when people are expiring on certain things and then doing a tiered system.
We are very optimistic about it. We think it’s going to be very successful in the operation, but what I’m hopeful for – and I think it’s a big area of improvement for our operations – is not just to teach the ‘how,’ but the ‘why.’
We really want to have tools that teach the ‘why,’ because as we’re dealing with workforce challenges, it’s easy to just say: ‘Hey, check the oil’ or ‘check the tire’ – the standard pre-shift run. But they don’t know ‘why’ they are checking the oil or ‘why’ they’re checking the tires.
SCOTT ALEXANDER (SUMMIT MATERIALS): I think getting back to basic ‘blocking and tackling’ is a good thing to change your safety culture. We’ve seen significant improvement even without the use of technology – and I’m not trying to say anything negative about technology. That’s great, too.
A couple of things we’ve done that probably could help everyone here: If you’re not already finding this, we’ve found a lot of injuries occur in the first 90 to 120 days of employment. So, we’ve assigned an employee in the plant to mentor every new hire.
If you’re a new hire and you are afraid to go to the plant manager, you don’t want to look like you don’t know what you’re doing. But if you have a mentor who’s looking out for you, that makes a big difference.
We’ve tripled the amount of onboard training from a safety standpoint. We go three days, and they don’t hit the plant until they’ve done that.
RONALDO DOS SANTOS (ANDERSON COLUMBIA): I think you can use any type of technology, but if people are not aware of the hazard, then the safety will be compromised.
One thing we’re focused on is training for midlevel supervisors. We promote a lot of people from the ground up. You start as a laborer and then become a groundman, and then they have a leadership position. So, they might not be prepared to coach skills and hold people accountable. We’re addressing that area of training for midlevel supervisors.
On new employees: We have mandatory in-shop training. After that, the job is not done. We developed a safety committee, which is employees who are a little bit more experienced – two to five years – so they can help us to onboard new employees. It’s not directly supervised so they are comfortable. We hope to share some of our concerns with the safety committee.
This aspect never goes away, even if you incorporate technology.